HMMA 10th Anniversary
On May 20, 2015, Hyundai Motor Manufacturing Alabama, LLC (HMMA) completed its 10th year of producing high-quality cars for the North American market. HMMA’s records, awards, and successful model launches would not be possible without the dedication of so many hard working Alabama Team Members. To celebrate these remarkable 10 years, a group of Team Members chronicled their experiences and the impact HMMA has had on their lives. We hope you enjoy their reflections on this amazing place.
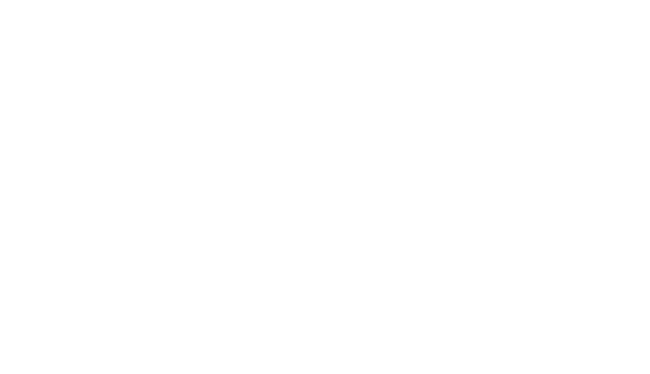
Chris Weihe
Stamping maintenance Team Member Chris Weihe joined the Hyundai family...
Pat Means
Pat Means has been an HMMA Team Member in general...
Cheryl Trone
Paint shop Team Member Cheryl Trone became an HMMA Team...
John Hall
Engine maintenance Team Member John Hall has been at Hyundai...
Alicia Phiffer
Team Member Alicia Phiffer is approaching her tenth year at...
Benny Phillips
Team Member Benny Phillips joined the HMMA family nearly 11...
Cedric Sankey
Cedric Sankey is a production Team Member in the stamping...
Jeremy Richardson
Team Member Jeremy Richardson works on the trim final line...
Sally Wren
Team Member Sally Wren is a specialist in the payroll...
Joseph Bradley
Joseph Bradley works on the chassis 1 line in general...
Kyle Waites
Kyle Waites joined the HMMA team in January 2005 as...
Sharon Robison
Sharon Robinson has been an HMMA Team Member since November...
Calandra Mills
Calandra Mills is a Team Member in the weld shop,...
Charlena Mack
Charlena Mack has been a Team Member on the door...
Randy Williams
Randy Williams is a quality process evaluation specialist in the...
Krista Hawkins
Krista Hawkins is a community relations specialist in HMMA’s public...
Donna Lenning
Donna Lenning works on the BC1 line in the weld...
Johnny Shaw
Paint shop team leader Johnny Shaw joined the HMMA family...
Kim Abrams
When Kim Abrams first joined the Hyundai team in January...
Shon Hunter
Stamping shop Team Member Shon Hunter has been at HMMA...
Chris Weihe
Chris Weihe:
Stamping maintenance Team Member Chris Weihe joined the Hyundai family nearly 12 years ago on August 18, 2003. When Chris first came to work at HMMA, the landscape looked a lot different. “It was still dirt out here,” he said. “The weld shop had a roof, but they were pouring concrete and setting the slabs under the roof. In the stamping shop they were in the process of putting the roof on.
“Where the parking lot is now, there were a bunch of trailers, and the maintenance office was out there,” Chris remembers. “We would walk out to the plant site to see how things were progressing, and once the equipment started coming in we started checking the machinery.”
Over the next two years, Chris and his fellow Team Members watched as HMMA’s shops took shape. The stamping shop was cranked up to begin the process of transforming rolls of steel into the car body panels that would go on to become Hyundai vehicles.
“When we started up, we were running at about seven strokes per minute while everyone was working to get things just right with the tooling,” Chris said. “Compare that to now, when we have some parts we can run up to 11 strokes per minute.”
No matter how slow things may have been to start, Chris says it was a rewarding experience to see the assembly process in action. “It felt good that we were in operation,” Chris recalls. “We were making vehicles prior to that but they were test vehicles. It was amazing to see the real cars in the various stages of production.”
And now, 12 years later, when he sees an Alabama-built Hyundai on the road, Chris says that good feeling is still there.
“There’s a sense of pride when you see a Sonata or Elantra on the road because you know it came from this place,” he says. “If you’re in maintenance you know you helped keep the equipment in operation to make that car, and it’s a quality vehicle.”
Thanks to dedicated maintenance Team Members like Chris, HMMA’s first 10 years of production have run like a well-oiled machine.
Pat Means
Pat Means:
Pat Means has been an HMMA Team Member in general assembly since January 4, 2004. When she began her tenure with Hyundai 11 years ago, she was among the first group of HMMA Team Members that were sent to Korea for a month of hands-on training.
“We were in Korea for 34 days,” Pat recalls. “It was the first time I was away from my son, and it was a culture shock, but the people there were so kind to us.”
The on-the-job training provided these Team Members with a set of skills they would need to come back and help train their coworkers. They learned everything about how to assemble a vehicle, down to the basics like knowing the best techniques for holding a tool or bolt.
When Pat came back to Alabama, she was promoted to team leader in the Trim area. There, she and her fellow Team Members had the unique responsibility of determining which tasks would be completed at each work station.
“We had to determine the order for every part to be put on, so that, for instance, you wouldn’t be putting a patch on and then have to take it back off later to put a screw underneath it,” she said.
It was a huge task, but Pat knows the work they did back then truly laid the foundation for a successful and efficient assembly process on the trim lines, where she is now a group leader.
“It makes you feel proud to know that what we did has contributed to all of HMMA’s milestones, like the first car, or the first million cars,” said Pat.
When she reflects on her years at HMMA and all those milestones she has helped achieve, Pat says she’s thankful to be a part of the Hyundai team.
“Before I came here, I was struggling and trying to make ends meet for me and my son,” she remembers. “I have been blessed now that I don’t have to wonder how I’ll put food on the table. We’re all here to provide for our families, and it’s important to remember that we’re working for them when we come to do our jobs every day.”
Pat’s motivation and dedication to building a vehicle of the highest quality is a characteristic shared by many Team Members, and it’s what makes HMMA a truly remarkable place.
Cheryl Trone
Cheryl Trone:
Paint shop Team Member Cheryl Trone became an HMMA Team Member on November 15, 2004.
When she first joined Hyundai over 10 years ago, she started off in the black tape area of the paint shop where she still works today. Remembering back to that time, Cheryl recalls how different her average workday was then compared to now.
“Back then, we usually built one car a day,” Cheryl says. “We did lots of cleaning and touring the different areas of the paint shop to learn about the processes. One day we worked a voluntary Saturday shift, and maybe 19 or 20 cars came down that day. We were so excited!”
Cheryl says the process of applying black tape is one that takes finesse and practice, and at first it was no easy task.
“It really is an art to apply the black tape,” she explains. “We had to learn to put it on while the car was standing still, and then there was a whole new level of difficulty once the car was moving on the assembly line. We had Team Members from Korea here to train us on how hold the jig correctly and maneuver the jig so the tape wouldn’t crinkle. It became so much easier once we learned to do it the right way, which was important as we began to build more cars every day.”
That number of cars per day has steadily grown over the years from one a day in 2004 to over 1,550 today. Despite the difficult nature of the task, Cheryl says she wouldn’t want to work any other job at HMMA.
“The black tape, to me, is the first thing the customer sees when they walk up to the car door to get in,” she says. “When we see an Elantra on the road, I love pointing out the tape and showing my kids exactly what I did to help build that car.”
Cheryl is as proud of her workmanship as she is to work on the Hyundai team. “I’m so thankful to work at Hyundai because it has given me so many opportunities I didn’t have before,” she said. “I was able to buy my own home and now I’m putting my daughter through college. I got to go to Korea in 2008 and it was my first time ever on an airplane.”
Beyond all the new experiences and opportunities, however, Cheryl says her time at HMMA has been enhanced the most by the great people she has met and the Team Members she works alongside every day. These Team Members are truly the key to the past 10 years of success at HMMA and many exciting years to come.
John Hall
John Hall:
Engine maintenance Team Member John Hall has been at Hyundai since October 18, 2004, when he was first hired to work in the engine assembly department.
“When I started, we weren’t building any engines yet,” he remembers. “All the equipment was still being installed, and we were checking the different workstations for safety and deciding where parts should be stationed on the line for assembly.”
Gradually, the engine shop ramped up production, and soon John found himself with an opportunity to move from production to maintenance.
“I had 25 years of experience in maintenance previously, so I was excited to get a maintenance job here,” he said. “It’s given me a chance to learn a lot about automation and logic with all the different types of robots we use.”
In his 10 years on the Hyundai team, John has been a part of the many milestones HMMA has achieved, but he says one stands out in his mind as the most exciting.
“When we built our millionth car, I was so proud,” he recalls. “If you build a million cars, that means someone had to have bought a million cars! Knowing there were a million people out there driving a car I helped build gave me a super sense of pride.”
John’s not only proud of the cars he builds, but of how working at HMMA has enabled him to provide for his family in new and better ways. “I’m able to have great benefits for my family, and we’ve been able to buy a nice home in a safe neighborhood,” he says. “I don’t feel bogged down by debt and I feel secure for the future.”
John knows that the future is bright for Hyundai and its Team Members. He says, “If we continue on our current course, the sky is the limit for how great we can be!”
Alicia Phiffer
Alicia Phiffer:
Team Member Alicia Phiffer is approaching her tenth year at HMMA, having worked in the weld shop since February 2006.
“When I first came to Hyundai, we were building about 200 cars a day, but some days ran faster than others,” she remembers. “Everyone was like a big family and we all worked together to make sure we could keep the line running.”
Alicia’s first job as a Team Member was working the right side line, where she stayed for almost a year before moving to the left side. “Back in 2006, working the side line in the weld shop meant you would pick a part for the robot and then position it for the robot to do the welding,” she recalls. “On the right side of the car that was pretty simple, but then on the left side you had to also make sure the fuel fillers were loaded and install the combi lamp, too.”
Nine years later, Alicia is now working on the roof sub line where the roof rails are welded, and the process is a lot more advanced than in previous years. “Now, instead of holding the parts to be welded ourselves, we load the roof rails onto a shuttle for the robot to pick up,” she explains. “The robot positions them and we monitor the process, making sure there are no bad parts being sent to the robots and that the robot is welding everything correctly.”
Alicia says she has gained a wealth of knowledge during her time in the weld shop, and she loves working on roof sub. “I feel so confident in my job now,” she says. “I have enough experience that I can handle most problems I see or robot faults that happen, but I also know that I will be able to learn how to resolve any new faults I haven’t seen before.”
While so much has changed during her time at HMMA, Alicia says there is one notable thing that has remained the same. “The family environment is still the same as it was nine years ago,” she says. “I have met new people and learned about so many different cultures, and I’ve been able to provide for my family at home, all while feeling like I’m part of the big Hyundai family, too.”
Benny Phillips
Benny Phillips:
Team Member Benny Phillips joined the HMMA family nearly 11 years ago on May 24, 2004. He worked for production control driving a forklift – a job that took him to every shop at one time or another.
“Back when I started in 2004, the buildings were up but everything wasn’t inside yet,” he remembers. “It was dark because the lights weren’t in yet, so we worked with just the light from the emergency lighting.”
Benny spent his first four years at HMMA on a forklift, which has given him some fun memories. “I remember that the roads weren’t paved yet and the forklifts would get stuck in the gravel, and they’d have to pull them out with a boom lift,” he laughs. “I also remember being the first person to use the freight elevator to take a forklift the second floor of the paint shop when I hadn’t even known that was possible.”
In 2008, Benny saw an opportunity for a Team Member transfer to the Dyno Lab in the engine shop where durability tests are performed on HMMA-built engines. “I have a degree in electronics, so when I saw the job posting I was really excited about the possibility of a challenging new experience,” he says.Benny got the transfer and started working in the Dyno Lab testing engines alongside three other Team Members that he’s still working with today. “Scott Bashaw started in the lab the same time I did, and we were trained by Randy Mosley and Milton Jones,” he recalls. “The four of us are still here together.”
Aside from the opportunity to learn about engine testing in the Dyno Lab, Benny said working at HMMA has brought him several opportunities he wouldn’t have had otherwise. “When I started in 2004 I was thinking about sending my daughter to college one day,” he says. “Now here I am, about to send her to AUM in the fall, and I’m able to do that thanks to my job at HMMA. I’m proud that we all have an opportunity to plan for our futures with a little help from Hyundai.”
Cedric Sankey
Cedric Sankey:
Cedric Sankey is a production Team Member in the stamping shop. He joined HMMA 11 years ago, back in July 2004.
“When I started, we were mostly cleaning and training,” Cedric remembers. “It took several months for all the equipment to be installed and all along we were thinking, ‘How will we run all this?’ I remember wondering if I’d get a chance to try.” Even the Team Members in stamping looked a little different back then, he says. “We had to wear hard hats at first, before they introduced bump caps,” he laughs. “I felt like I was wearing a football helmet all day!”
Once things got up and running, Cedric and his fellow Team Members found themselves doing many of today’s automated processes by hand. “None of the automation was in place yet, so we had to do things like move panels ourselves,” he says. “We would take the blanks off the blanking press by hand and stack them on a forklift, then the forklift would drive them to the stamping press and we’d load them into the press by hand.”
Cedric says that in all his time as a Team Member, those automated processes have made a huge difference in the stamping shop, but it’s still up to the Team Members to keep everything running smoothly. “Working on the blanking press, I know the stamping press is my customer, so I’m going to work hard to meet my customer’s needs for that day,” Cedric says. “If I’m giving 100 percent, and the next Team Member is giving 100 percent, and we’re all making our maximum effort, then we know we’re going to meet our goals.”
Jeremy Richardson
Jeremy Richardson:
Team Member Jeremy Richardson works on the trim final line in general assembly. He has been a Team Member for one year, but began his tenure at HMMA as an Aerotek employee back in January 2013.
“I’ve worked on the trim final line for the whole time I’ve worked here,” Jeremy said. “Mainly I work at station 3 where we take the couplers off the car and put in the brake fluid and coolant, but I know all the jobs on trim final except for two.” Jeremy learned many of those jobs while he was still a contractor working for Aerotek at HMMA. He said the opportunity to be hired on as a permanent Team Member was a huge accomplishment. “I worked hard for Aerotek, I didn’t miss any days, and I even helped train some of the Team Members who were going to be working with me, “he recalls. “I feel like that dedication is what helped me get hired on permanently. I’m so happy to be a Team Member now and to be part of the Hyundai family.”
Jeremy said being in the Hyundai family extends beyond the work day. “I have made so many friends here,” he said. “I see my work friends outside of work and even go to church with several of them.” While Jeremy’s time here has been short compared to HMMA’s 10 years of production, he said he can see himself growing with the company for the long term.
“I see myself moving up within the company, to maybe specialist or even a member of management,” he said. “There are so many great opportunities here and I want to work toward that.
“To my fellow Team Members: keep up the good work, but don’t forget to be appreciative and grateful. This is a great company to work for.”
Sally Wren
Sally Wren:
Team Member Sally Wren is a specialist in the payroll section of the HR department. She joined HMMA in June 2003 and has been processing Team Member payroll ever since.
“Back in 2003 we didn’t even work at the plant site,” she says. “We worked from offices in East Montgomery. There were about 35 total American employees at that time working with about 50 Korean colleagues.”
When Sally first started processing HMMA’s payroll, the job was a lot different than it is today. “At first, payroll was done manually with paper time sheets,” she remembers. “There were no deductions yet for benefits, like the 401(k), it was just straight net pay, taxes, and gross pay.”
In 2005, the Administration building was the first to be finished at HMMA and the team working from East Montgomery finally got to come to work at the plant site.
“The whole area was still considered a construction zone,” Sally recalls. “When we got to work every morning, we had to walk from our cars to the building wearing hard hats and steel toe shoes. The parking lot was still a cow pasture so we walked over boards on the ground to stay out of the mud.”
Once HR was up and running in the Admin building, things began growing rapidly. “We had the first big wave of hiring for Team Members and we had to learn to process their payroll using a new payroll system,” she says. “It was and still is a little nerve-wracking to know that you’re responsible for making sure everyone is paid on time with no errors.”
Now, in 2015, the payroll process is much more complicated but also much more automated. “We have so many deductions now, but we also have the automated time system, and that automation has been key to getting more than 3,000 people paid correctly and on time.”
But more than that, Sally says the people on her team are what have kept the payroll processing smoothly. “I have the best department. I’ve been with these people forever and the teamwork is outstanding. We complement each other and they are just a joy to work with every day.”
Joseph Bradley
Joseph Bradley:
Joseph Bradley works on the chassis 1 line in general assembly and has been an HMMA Team Member since July 2012.
“We install brake lines, fuel tanks, the washer fluid reservoir, heat shields, and other parts,” he said. “And for about the last year and a half I’ve worked as a keeper on chassis 1.”
As a keeper, Joseph has to stay focused on quality at all times, and he said the high quality at HMMA is something he wasn’t expecting.
“Before I started working here, I only knew about Hyundai’s past,” he recalls. “Once I started working here I realized both the design and the quality of the cars really exceeded my expectations.”
Not only did his expectations change since he began working for HMMA, but Joseph’s life has changed, too.
“I have a new baby, and it has completely changed my outlook about my job,” he said. “I have to be even more focused on quality so that I know I’m secure in my job since I have someone else to take care of now.”
But Joseph said it’s not hard to produce a top-quality product when he’s working as part of such an amazing team.
“I love the teamwork on my line,” he said.” Most everyone is trained well in multiple jobs and my teammates are always ready to help if an issue arises that we need to address. If you don’t know the answer, it’s almost guaranteed someone nearby does.”
And whether it’s taking on a challenge or working alongside a great team that keeps you motivated, Joseph says it’s important to find your own inspiration for keeping quality high. He says, “Find something you like about every job you do and let it help you stay focused so your quality will never falter.”
Kyle Waites
Kyle Waites:
Kyle Waites joined the HMMA team in January 2005 as a production Team Member in the paint shop on the sealer deck.
“Back then we were running pilot vehicles, and only about five a day,” he recalls. “We did a lot of cleaning and a lot of waiting, and for a few months we practiced on dummy units during the breaks between pilot cars.”
That practice paid off as vehicle production ramped up and the number of cars on the assembly line began increasing.
“There were days we ran around 90 units and it was astonishing,” Kyle says. “The day we broke 100, I was amazed at how it was possible. Before that I could never really envision that kind of capacity.”
In his 10 years at HMMA, Kyle has watched production ramp up from 5 cars a day to over 1,500 a day, all while he has seen his own career flourish as well.
“I became a team leader in November 2005, then a group leader in 2008, an assistant manager in 2011 and then a manager in 2012 when the third shift was added,” Kyle remembers. “Having these leadership opportunities has been the most rewarding part of my experience at HMMA because it gives me the opportunity to develop other team members and help them reach their own career goals, too.”
Kyle says the past 10 years have not only impacted his personal experience, but he’s seen how the high-quality vehicles being built at HMMA have had an even greater influence on Hyundai’s global identity.
“In 10 years I’ve seen the transition and impact that Hyundai as a brand has made in the marketplace,” he says. “HMMA has made a huge impact on Hyundai’s ability to establish a positive brand image here.”
Ultimately, Kyle says he’s proud to work for a company where he knows the sky’s the limit. “This job takes commitment,” he says, “but there are always new opportunities.”
Sharon Robison
Sharon Robison:
Sharon Robinson has been an HMMA Team Member since November 2004. She currently works in engine shop No. 2, but she started off in general assembly.
“When I first started here, I was working on trim 3,” she remembers. “We weren’t building cars yet, so we spent a lot of time training. We learned how to do the processes within that time and we did lots of stretches and exercises to teach our bodies how to handle the physical aspects of our new jobs.”
Soon, Sharon says her team began getting more hands-on training. “We practiced on dummy cars so we could learn how to use our tools in the most efficient way,” she recalls. “We had to learn the best way to hold the part and use the tool so that we could get the job done in time.”
Sharon loved her time in trim, but she’s also a person who’s always looking for new experiences and learning opportunities. After 8 years, Sharon transferred to the engine shop. At first she worked in machining, and then later she moved to assembly where she works today.
“I have liked all my jobs, but I like this one the best,” she says. “I have learned so many new things, like how to fix the machines when they go down. I get to be a keeper sometimes, and have had the opportunity to run head sub. I love learning new things about my job.”
While Sharon says those learning opportunities are probably her favorite thing about working at HMMA, she also says there are plenty of other reasons she loves coming to work every day.
“From my heart, I am grateful for Hyundai,” she says. “My husband, my son and I all work here. Hyundai is always providing for us, and the people here are such good people. It’s a company to be thankful for.”
Calandra Mills
Calandra Mills:
Calandra Mills is a Team Member in the weld shop, working on the BC1 line. She joined the HMMA family back in February 2006 and is quickly approaching her 10-year anniversary with the company.
“When I first started at HMMA, the plant had just achieved the 1,000 vehicle-per-day milestone,” Calandra recalls. “I started in moving parts, and at that time we were working 10-hour shifts. I had never worked a 10-hour shift before so that was a big adjustment.”
Calandra says a longer shift was not the only adjustment she made when she began working at HMMA. “Before Hyundai, I worked in medical collections,” she says. “I knew I needed a change; I wanted something different so I could branch out a little. I applied for a job at Hyundai and decided that I would do anything they asked me to do. If they would hire me, I’d do my best at anything.”
Calandra’s enthusiasm paid off, and once she got her job offer and completed her training, she learned exactly what that “anything” would be.
“They read out our names and told us we’d be in the weld shop, and I didn’t know what that meant,” she laughs. “I imagined people doing all the welding with a torch and the big weld mask on, and I had no idea what I’d gotten myself into.”
Now, nearly 10 years later, Calandra is very happy with her role in the weld shop and says any time things get demanding she thinks back to her initial enthusiasm and keeps that do-anything attitude.
“Remember how it felt when you first got hired and how excited you were to do whatever Hyundai needed as long as you could get the job,” she says. “Even when things get stressful, continuing to be grateful will help get you through it.”
Charlena Mack
Charlena Mack:
Charlena Mack has been a Team Member on the door sub line since June 2005. Charlena used to work in retail, so she says working at HMMA came with quite a learning curve.
“It was such a challenge at first, and sometimes I still face those challenges,” Charlena said. “It’s hard to work and talk at the same time, and people thought I was being anti-social, but my teammate Kiian helped me learn to open up and be social while still staying very focused on the job at hand.”
She works a variety of jobs on door sub and says she could never pick a favorite because they all have their own merits. “I love the whole door line,” she says. “But more than the jobs, I love working with all the people on my team. If you have an issue you always know someone will be there to help you.”
Over the last 10 years, Charlena said her team on the door line, and the Hyundai team as a whole, has been much more to her than just a group of coworkers.
“I moved here with my husband and son, without any family in the area,” she said. “A few years ago my husband passed away unexpectedly, and since then Hyundai has truly become my family. People I didn’t even know offered me condolences, and now out in the community other Team Members will speak to my son and look out for him. I am so blessed to have this job and these people.”
Charlena says HMMA is blessed to have Team Members who are both hard workers and great people, and that’s what truly makes this a wonderful place to work.
“We all come from different backgrounds, but we are all here with the same goal: to build a quality car,” Charlena said. “What makes Hyundai great is that we get to work towards that goal with friends who feel like family.”
Randy Williams
Randy Williams:
Randy Williams is a quality process evaluation specialist in the quality assurance department. He has been a Team Member since October 2006.
“When I first started, I was working in body quality control in the CMM lab,” he recalls. “At that time we were building the Sonata and Santa Fe, and we would pull two vehicles a day for quality checks on the coordinate measuring machine (CMM).”
Randy said the machine would have to measure 13,000-18,000 points per vehicle to evaluate body quality, and that was a time consuming process. Over time, that evaluation process evolved and improved.
“The biggest innovation was when we began using laser scanners to scan the parts,” Randy says. “The laser can look at moving parts better than the CMM, and we can even take the laser to the production floor to check things out. Plus, we can let the CMM run while we use the laser scanner elsewhere, increasing the volume of quality checks we can complete.”
In 2013, Randy moved from body QC to the quality evaluation department, which is now called quality assurance. He says over his time here, he’s watched Team Members grow to understand how they can build quality into the cars every day.
“We’ve been doing this a while now, and our Team Members have learned what it takes to build a car and how their process affects the next process and the overall product,” he says. “Everyone has a customer, whether it’s at the next station or the end of the line, and our Team Members really care about sending high quality to their customer.”
Krista Hawkins
Krista Hawkins:
Krista Hawkins is a community relations specialist in HMMA’s public relations department. She joined the HMMA team in early 2005 as a contracted HR recruiter, and then became a PR Team Member later that year.
“When I first became a Team Member I was a protocol specialist which meant I gave plant tours and did other projects in the visitor center,” Krista says. “For my very first tour, a group accidentally showed up on the wrong day and the rest of the PR team was at the training center. I was nervous, but I put them on the tram and gave them the best tour I could.”
Over time, Krista’s responsibilities grew to include the administration of HMMA’s community relations activities. In 2007, she officially became a community relations specialist.
“Back then, HMMA had diversity activities separate from community relations activities,” she remembers. “Diversity coordinated activities like Habitat for Humanity while community relations sponsored activities like the Joy to Life Walk for Life.
“When I started in community relations it was my goal to have those two functions working together so that HMMA was sponsoring activities as well as being present for the events. Today, that is a reality and HMMA’s presence in the community is much more visible.”
Krista says over the years HMMA’s community relations initiative has grown exponentially and it’s due in no small part to Team Member involvement.
“Hyundai is a leader in corporate giving in the River Region, and our Team Members are leaders in giving of themselves,” she says. “We are a team both inside and outside HMMA, and our Team Members are amazing at doing good, showing up, and giving back to our community.”
Donna Lenning
Donna Lenning:
Donna Lenning works on the BC1 line in the weld shop. Her 10-year anniversary with HMMA is quickly approaching as she became a Team Member in November 2005. Donna says she had some experience in automotive and manufacturing before she came to HMMA, but she still had quite a learning curve to overcome in the weld shop.
“I came from a plant that made seat adjusters, and I’ve worked in plants all my life, but HMMA is bigger with lots more people,” she says. “When I first started I spent just two or three days training and then I had to jump right in putting on fenders.”
Donna says it took about a month before she really felt confident doing the work on her own. “There were so many things you had to get just right,” she remembers, “like making sure the gap and flush were correct and then adjusting them if not.”
Back in 2005, Donna says the biggest challenge in her eyes was that the BC lines were constantly moving but the assembly line floor was not, so Team Members had to walk along to complete their tasks. “It was very difficult to do those processes while walking beside the car,” she recalls.
A huge improvement came when each station was equipped with a button to press once the task was finished. “Now, the cars all shuttle forward, then we complete the process while standing in place and press a button when our task is complete,” Donna says. “Once all the buttons have been pressed, the cars can shuttle forward again.”
Donna knows these types of plant improvements make everyone’s job a little easier, but it’s the Team Members themselves who can really step up and make a difference. “Be committed to doing your best at your job,” she says, “and always be there to help others when they need it.”
Johnny Shaw
Johnny Shaw:
Paint shop team leader Johnny Shaw joined the HMMA family 11 years ago, in February 2004. At that time, he says his days were spent learning the ropes to prepare him for his job in paint.
“When I first started, we spent every day for about the first month down at the Training Center just learning the basics,” he says. “After that, we went to Korea for a month of hands-on training at an assembly plant there.”
Johnny says that experience was very valuable and enabled him to come back with the knowledge he needed to start working in paint repair. “We worked in dent repair, inspect and polish, and moist sand,” he recalls. “The training was great, and so was having the chance to see Korea and experience another culture.”
Upon returning from Korea, Johnny was sent to Trenholm State for more auto/body repair training, and then finally was able to take his place on the assembly line.
“When we first started working on real cars, we were building just three or four cars a day,” he remembers. “They slowly ramped things up, and we were feeling really proud of ourselves when we first started building 100 cars in a day. There were no more big gaps in the line and there was very little down time, and we knew we were really building cars.”
That, of course, is nothing compared to the 1,550 cars HMMA now builds each day, but Johnny says that early experience is what has made his team so successful now.
“Reducing overall paint defects is the one thing that has made the biggest impact on our day-to-day operations,” Johnny says, “and we’ve been able to do that through Team Member experience and learning from any past mistakes.”
Kim Abrams
Kim Abrams:
When Kim Abrams first joined the Hyundai team in January 2004, she began as a production Team Member in the weld shop.
“Those first few weeks we were at HMMA’s Training Center, and then we went to Korea for 30 days for training on the assembly line,” Kim recalls. “We got hands-on training there so we’d be able to come back and help train other Team Members.”
many different cultures, and I’ve been able to provide for my family at home, all while feeling like I’m part of the big Hyundai family, too.”
That experience proved helpful for the next several months as Kim and her team learned the skills they’d need to help start up production later that year.
“After a few months, we moved into the weld shop, but it wasn’t even set up yet,” she says. “We cleaned and helped install the equipment to get the building up and running.”
Kim started on the floor line, where she learned to run robots and even learned to weld by hand. But, a few months into her tenure, she was approached with an exciting new opportunity: “They brought me to a completely empty room which they said would be the tool room, and they wanted me to set it all up.”
Kim took on the tool room task and stocked it with all the inventory the weld shop would need. Then, in 2010, she was presented with yet another opportunity – this time, a move to the safety department.
“Now, in safety, I stock the PPE for the entire plant and I handle all of HMMA’s workers compensation cases,” she says. “I love that this job lets me help people with their work comp claims and help them find solutions if they have a problem.”
From the weld shop to the safety department, helping her fellow Team Members has always been part of Kim’s job here at HMMA. She says that’s just the Hyundai way. “I love the spirit of family here,” Kim says, ”and how you know that people will always be there for you when you need them.”
Shon Hunter
Shon Hunter:
Stamping shop Team Member Shon Hunter has been at HMMA for the last 10 years. When she joined the Hyundai family back in October 2005, she began as an inspector.
“We had to inspect the panels to look for any imperfections,” she says. “We would use an oil stone to rub across the panels and highlight any defects.”
Shon says the oil stone method worked fine, but as she and her fellow Team Members got better at the inspection process they were able to help develop new inspection techniques. “All the inspectors helped develop a new glove technique as well as a highlight booth that makes seeing imperfections a lot easier,” Shon says. “When they’re easier to find, we are able to catch more defects and contain them in the stamping shop.”
About four years ago, Shon moved out of the job of inspector and began working as a press operator. She says she’s had many new learning opportunities since taking on her new role.
“I’ve had to learn the process of restarting the press after it has a fault,” she says. “The hardest part is remembering all the different types of faults and knowing the very specific things you have to do for each one in order to restart the press.”
But Shon says opportunities like these are what makes Hyundai a place she loves to work.
“Hyundai gives us opportunities for learning and recognition and advancement, as well as opportunities to help the people in our community who are less fortunate,” she says. “We have great benefits and we are always getting the monetary achievement awards, and there are improvements being made all the time – like the break areas and bathrooms. Hyundai has made my life better.”